This item is eligible for free shipping
G10 fiberglass boards are made of a special glass epoxy laminate that has extremely high strength. G10 fiberglass is used in marine applications due to its superior strength, moisture resistance, and excellent electrical and fire insulation.
Fiberglass boards make excellent non-corrosive backing plates for high load deck hardware or bond to engine room bulkheads to hold mounting brackets. G10 boards are sold in 1/4 and 1/2 inch thickness.
G-10 is similar in strength and density to starboard, but because it is formed from epoxy resin, it bonds easily using most two-part epoxies.
Available in Backing Plate sizes and full sheets.
Technical Information
- FR-4 Grade fire resistance
- Low moisture absorption
- Rated to 285 F continuous operating temperature, will not melt at high heat
- Resists chemicals
- High impact strength
- High tensile strength
- High dielectric strength
- High flex strength and dimensional stability
Reviews for G10 Fiberglass Board
Verified Purchase
I can use it for a backing as a single sheet or laminate two pieces together for extra thickness and strength. I use it to reinforce the deck where I mount winches, cleats, air scoops, and other hardware. It will wear the teeth down on a steel Saber saw blade in a short cut. Use carbide blades, circle hole saws, and router bits.
Was this review helpful to you?
Bought the 6 pc package of the 1/4 x 12 x 12 plates. Drills easily. Miter saw cuts well. Even sands easily. Eats jigsaw blades like there's no tomorrow - best I found is using blades for cutting sheet metal, but that still only gets you about 10" per blade. Great material!
Was this review helpful to you?
Verified Purchase
My sailboat had no backing plates on any of the stanchions or railing fittings. I found these products perfect for this application. The boards were easy to cut and drill and due to there construction would not suffer from exposure or any water intrusion.
Was this review helpful to you?
Verified Purchase
I bought this to plug a hole in the dash of my boat. The previous owner had cut a hole and I needed to fill it. Worked perfectly.
Was this review helpful to you?
Verified Purchase
backer plate, plain and simple. I like how you can sand down the sharp edges of it to fit the contour of your application. It also drills easy, but it doesn't flex at all! Great backer plate, although if you're buying only one, the shipping will ding you. I found that a bit ridiculous.
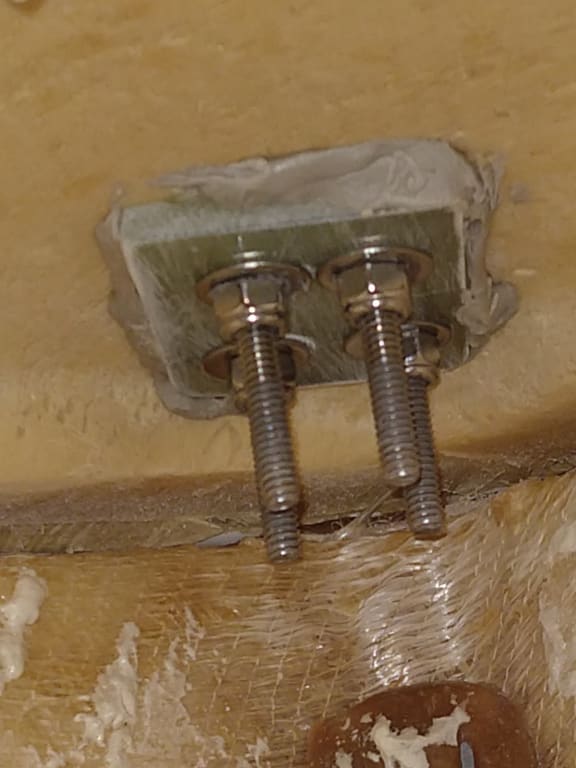
Was this review helpful to you?
Verified Purchase
Worked great for my use, replaced the bottom of my fiberglass boat exhaust. I used a jig saw to cut the material when through a lot of blades
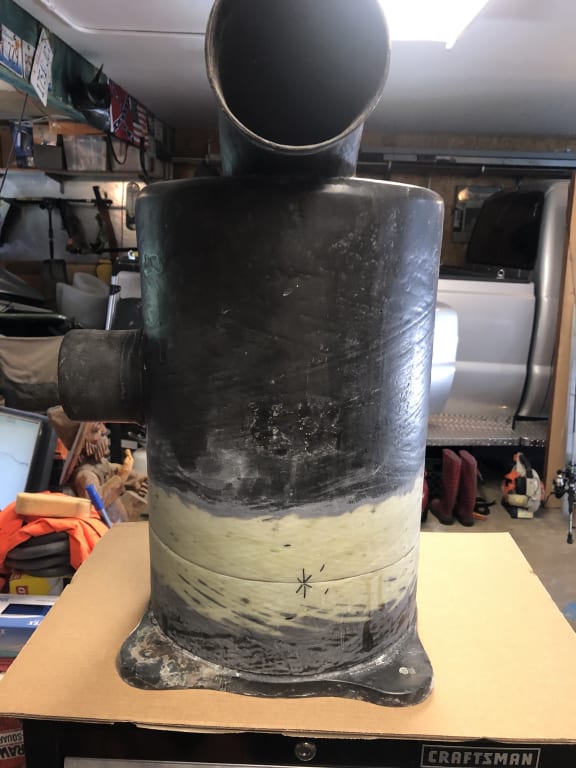
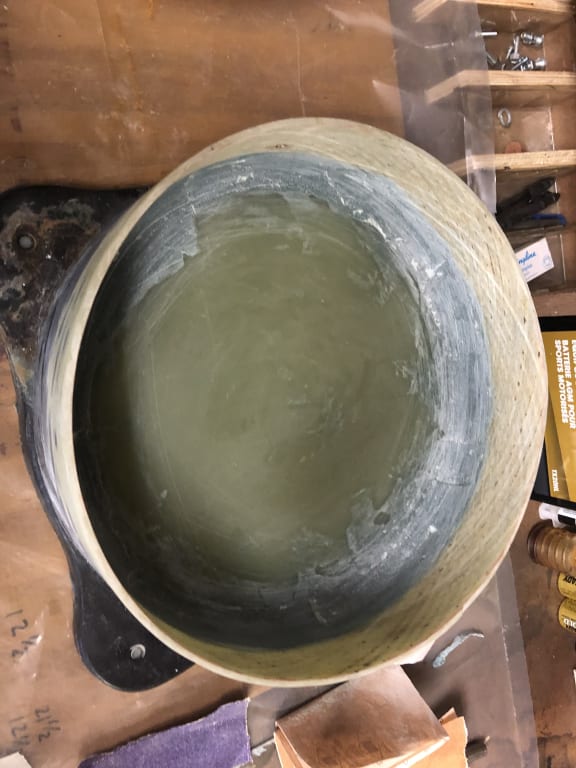
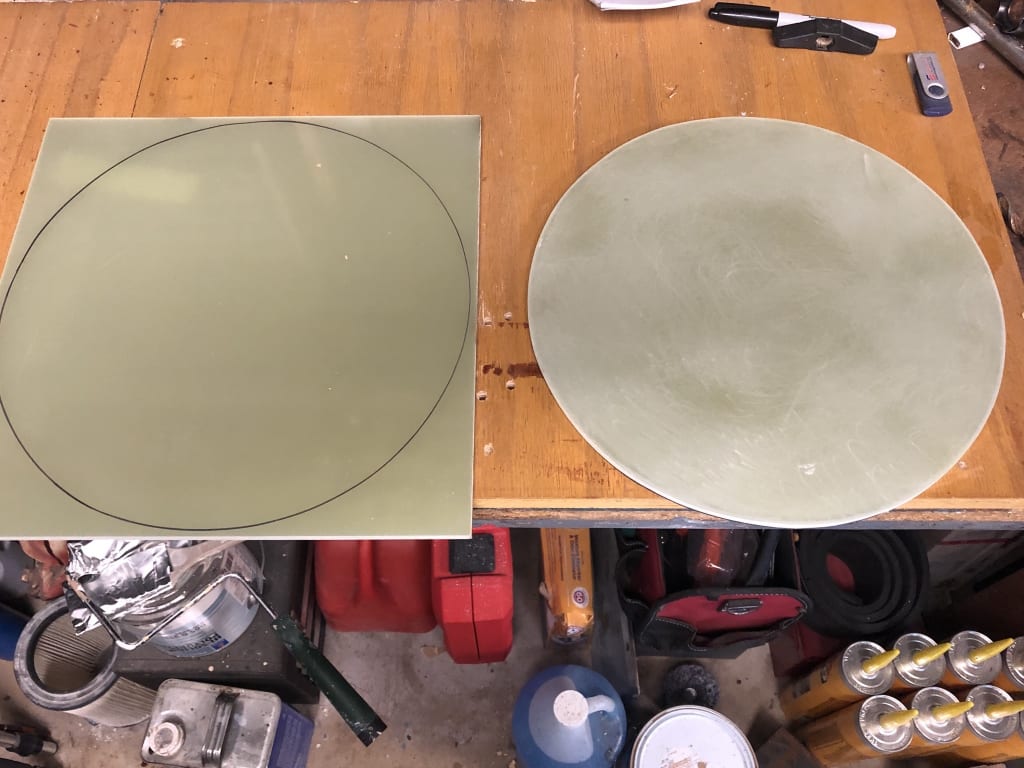
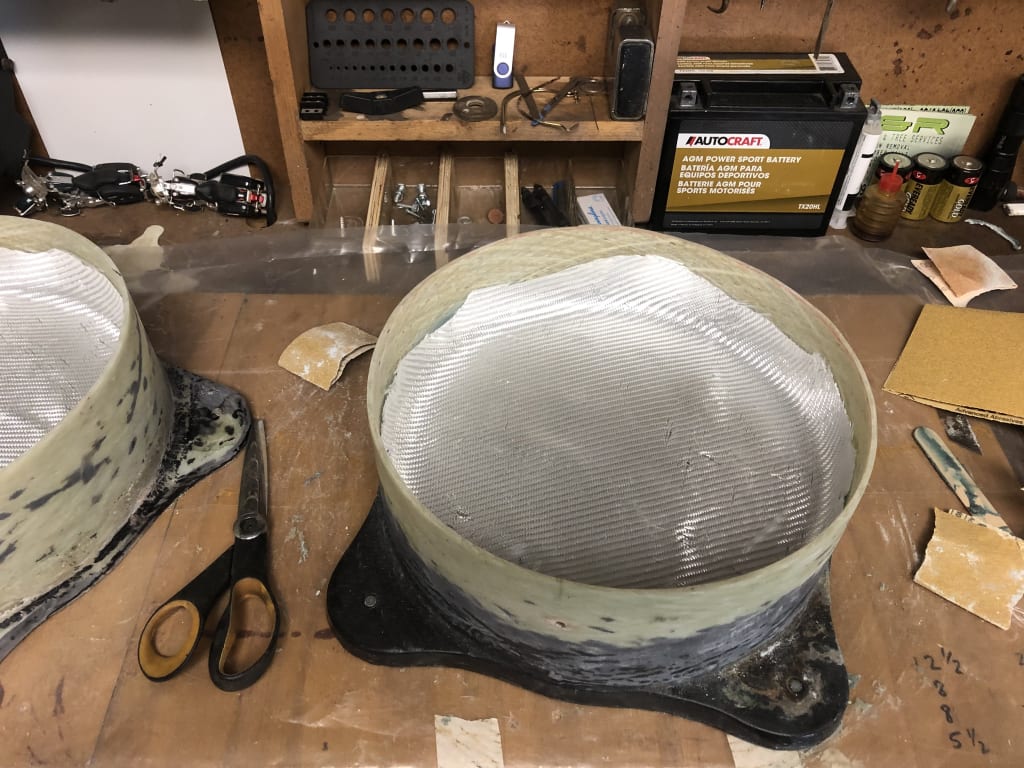
Was this review helpful to you?
I used the G10 board 1/4" thickness to replace the bottom of my wet exhaust muffler. It was perfect. I cut the 12"x12" x1/4" piece into an 11" diameter circle and glassed it in. I cut the material with a jig saw and finished the edges with a belt sander. It is hard and I did go through about 6 blades cutting out my piece. Expensive but worked great for my needs.
Was this review helpful to you?
I received my 12"x12" x1/4" piece and had to cut an 11" diameter circle out of it. I used a jigsaw. Burned up 12 Bosch jigsaw blades but it cut nice. Use a belt sander to finish it off. Very tough stuff. I'm using it to replace the bottom of my wet exhaust muffler. Nor I just have to glass it in.
Was this review helpful to you?
Verified Purchase
Great for custom helms
Was this review helpful to you?
Verified Purchase
Reasonable price, fast delivery.
Was this review helpful to you?