Tools & Inspiration For Craftsmen
Shop Now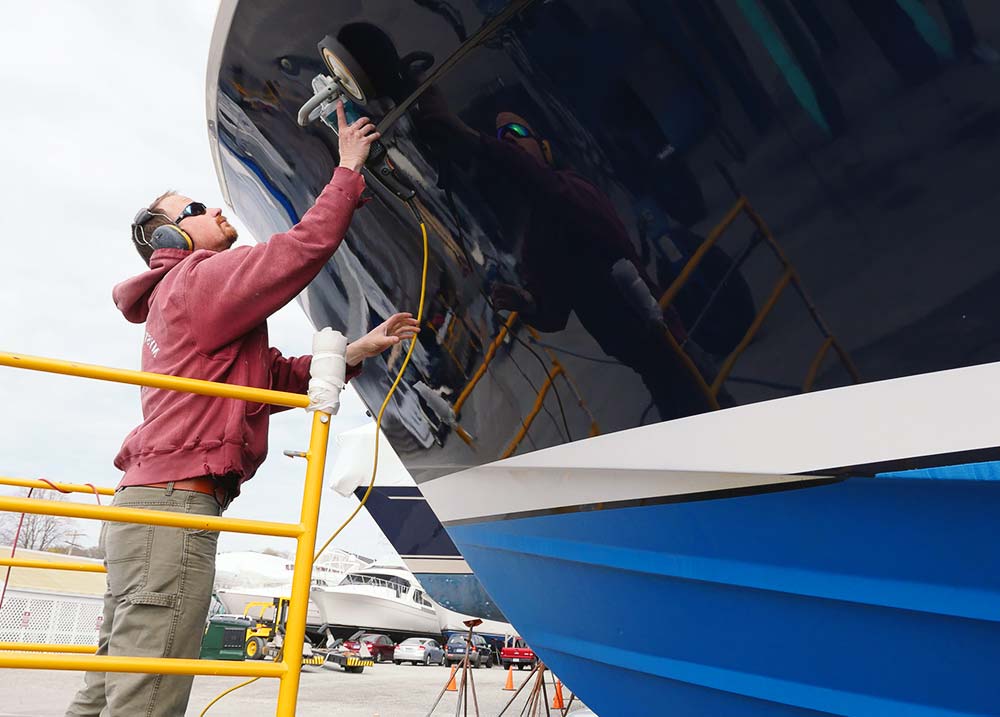
Totalboat
Explore the most comprehensive lineup of marine maintenance & repair solutions available. DIY makers & woodworkers prefer TotalBoat products for their ease of use and marine-grade durability
SHOP NOW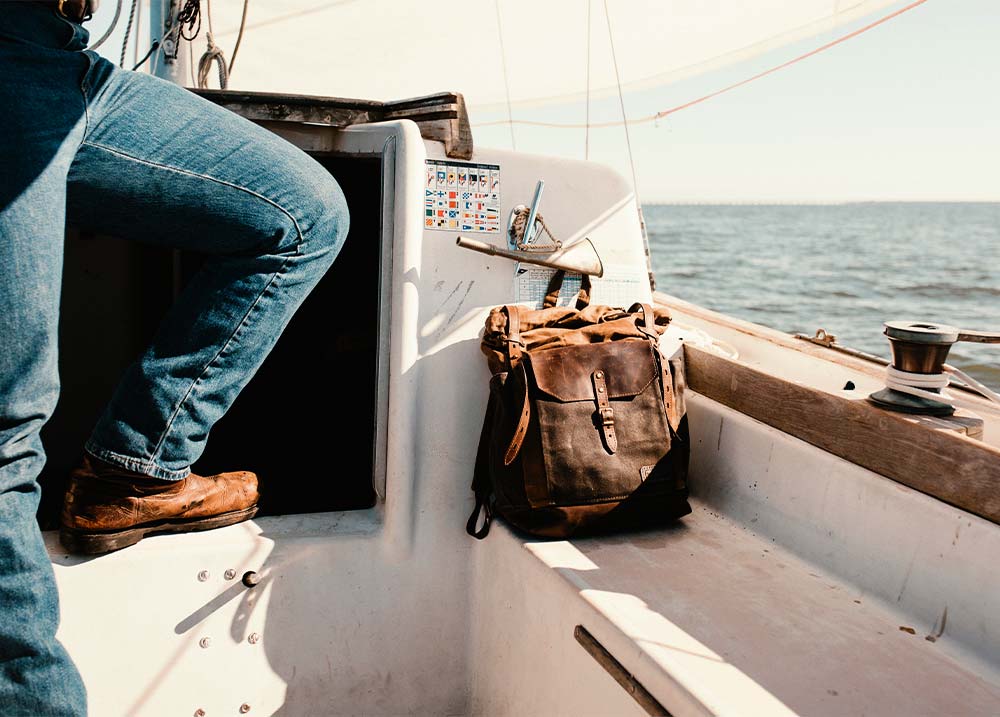
About Us
Our mission is to provide Tools and Inspiration for Craftsmen . We've been supplying building & maintenance products to boaters, builders & DIY makers since 1977. We love to help people build stuff!
Learn MoreFree Shipping!
Shop Now